The context
The search for a scalable replacement for copper as a thermal conducting material in high thermal management applications has been an ongoing process for over a decade. Copper is still useful as a thermal conductor – it’s cheap, effective, can be produced in large quantities and can be shaped for use on large components. But in certain cases, such as CERN’s Large Hadron Collider (LHC) and other specific industrial settings, there is a need for a material that possesses low density and can manage not only extreme heat, but also extreme structural pressure.
That is why CERN has, through various EU-funded projects and with the help of industrial partners Brevetti Bizz and Nanoker, been working on finding a suitable replacement. The work has centred on carbide-carbon materials (CCMs), which combine the toughness of carbides with the versatility of carbon, making them ideal as thermal conductors in tough conditions.
One solution, molybdenum-graphite (MoGr), has already been successful to some extent. It was initially devised for application in CERN’s upgraded High Luminosity LHC, which is scheduled to begin operations in 2030, as part of the collimators – devices used to control and shape the beam of particles.
These devices must operate very close to the particle beam and therefore have to dissipate significant power densities. A suitable and light thermal conducting material did not exist on the commercial market.
The goal was set to find a material that had: high thermal conductivity (two times higher than the best “standard” conductor, i.e. copper), good electrical conductivity, low density, low coefficient of thermal expansion and good mechanical properties.
After significant research and development of MoGr, teams at CERN managed to prototype and then industrialise the material, allowing in 2020 the construction of 15 collimators equipped with ~300 MoGr absorber blocks. Twelve of these collimators are actively being used during the current Run 3 of the LHC, which started in 2022 and will end in 2026.
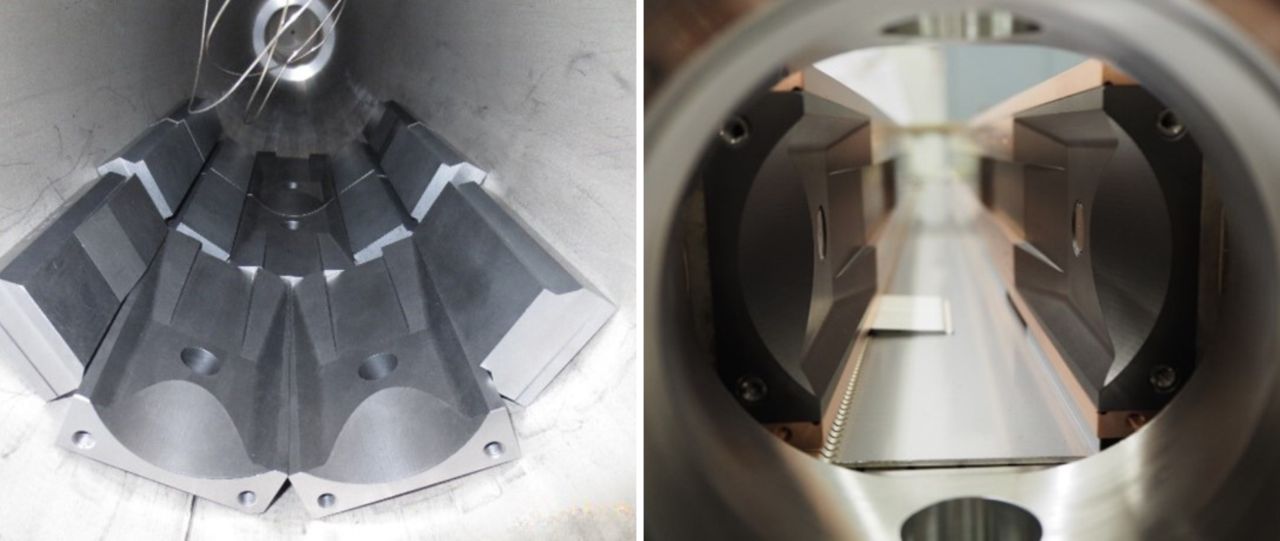
The challenge
The excellent thermophysical properties of the MoGr make it very appealing for a range of industrial and technological applications well beyond high-energy physics and colliders.
Potential fields of application for the material include high-power electronics, aerospace, fusion and nuclear fields, where reduced thermal expansion and low density are required along with high thermal conductivity and thermal shock resistance.
However, the extensive use of MoGr in industry and research centres has so far been hindered by its high production cost and the limited size of the blocks that can be produced.
When comparing good thermal conductors, high purity copper has a cost per unit volume of around €0.15 per cm3, isotropic graphite, which is lighter but less conductive, costs about 10 times more, and MoGr, lighter still and more conductive, costs around 100 times more than copper.
What’s more, the maximum size of a CCM part that it has been possible to produce has been limited to 400 cm3. Finally, the production process of such a CCM is energy consuming, requiring high machine power to reach the required sintering temperature, which is above 2600 °C. For these reasons, currently the application of CCMs can only be limited to very high-end applications, where the material cost is secondary with respect to performance.
The solution
The EU-funded I.FAST project, running from 2021 to 2025, is the latest to support work to find solutions for the limitations of CCMs, and facilitate their use in standard heat management applications. It was under the scope of some of I.FAST's predecessor projects, Eucard-2 and ARIES, that MoGr was first developed.
There are two ways in which CERN-based engineers are attempting to overcome the limitations of using CCMs more broadly: Reducing the sintering temperature and increasing the size of the CCM plates which are produced in each machine cycle.
A reduction of the sintering temperature provides several advantages. It is less energy and time consuming, and it allows saving components of the machine insulation that break at the MoGr sintering temperature and need to be replaced every cycle. On the other hand, increasing the size of the CCM plate makes it possible to produce more material per cycle at a very similar cost, and also provides an increased usable length for the finished components machined out of the plate.
The solution found during I.FAST has been to change the metal precursor of the CCM from molybdenum to chromium. Chromium forms carbides with graphite that allows sintering the material at much lower temperature than molybdenum. The obtained CCM, named chromium-graphite (CrGr), has been entirely developed within I.FAST, in collaboration between CERN and Nanoker.
Through several iterations during the project, Nanoker, with the technical support from CERN, managed to sinter CrGr plates twice the size as those achieved with MoGr (Ø230 mm, thickness 25 mm), at a temperature of 2000 °C against the 2600 °C of MoGr, with a 50% energy saving and without failure of any elements of the insulation systems, meaning that they can be re-used for future productions.
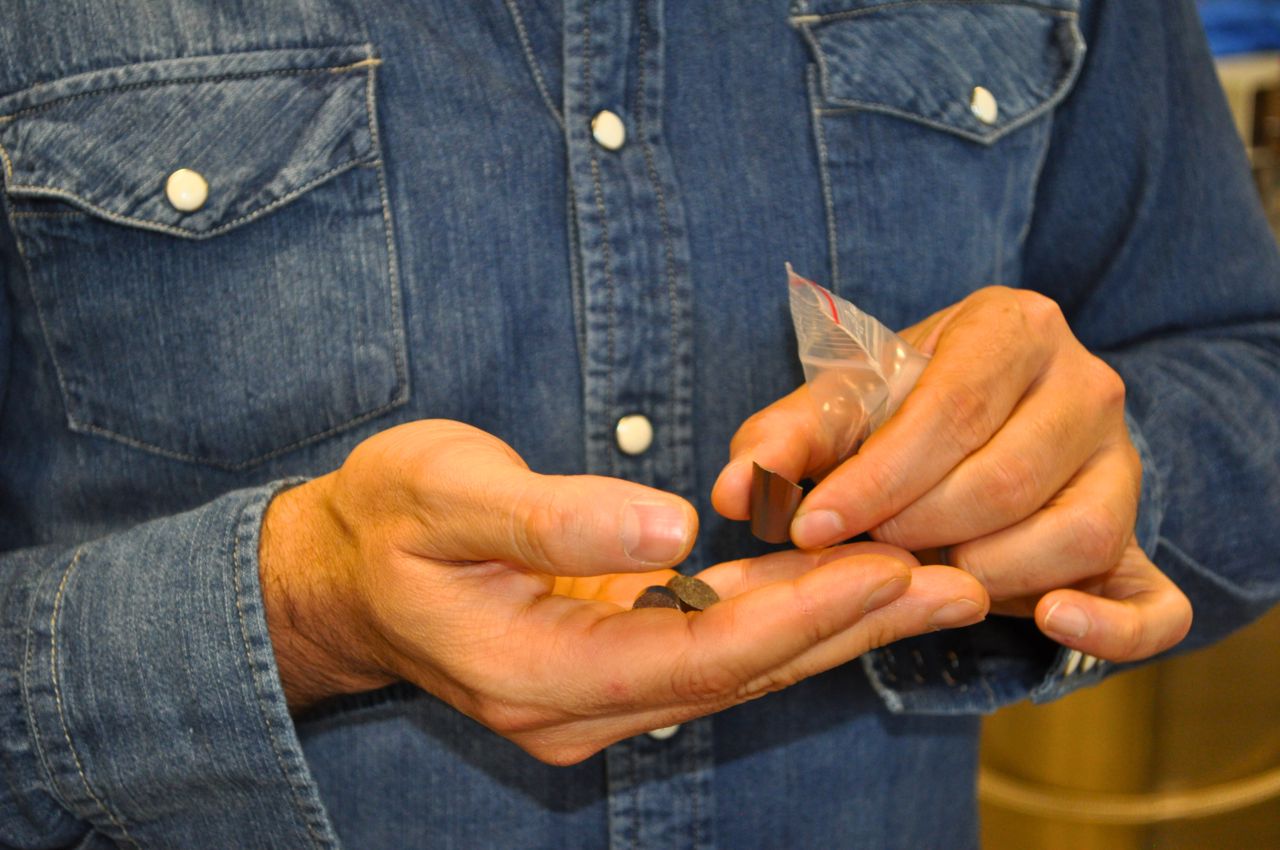
The I.FAST project gave scope to go further, not only producing the material, but also carrying out a detailed characterisation of CrGr to precisely measure its thermophysical properties as a function of temperature, and compare them with what was achieved with MoGr
This campaign was completed at CERN’s mechanical and materials engineering laboratory, which is equipped with state-of-the art machines can measure the coefficient of thermal expansion, thermal conductivity and diffusivity, specific heat, and mechanical properties in a range spanning from cryogenic temperatures (less than -270 °C) to more than 1000 °C. Each machine requires specific samples that were machined at Nanoker out of the sintered plates.
Such thermophysical measurements were backed up with additional tests done at CERN and at Nanoker, to probe other aspects of the material behaviour, for example its machinability to tight mechanical tolerances, its dimensional stability and its ultra-high vacuum (UHV) behaviour.
The results of the tests proved that CrGr is comparable, and in some respects even superior (dimensional stability and UHV compatibility), to MoGr, potentially opening up its use in industrial and research applications thanks to the lower production costs.
Additional possible developments may include the optimisation of the material and sintering parameters for large series productions, the development of faster and ad-hoc machining techniques, and the further increase of the plates for components of large size.
While challenges remain in refining production techniques and ensuring consistency across large-scale manufacturing, the advancements achieved through the I.FAST project highlight CrGr’s potential to become a cost-effective and high-performing thermal conductor, paving the way for its adoption in both cutting-edge research and industrial applications.
The I.FAST project has received funding from the European Union’s Horizon 2020 Research and Innovation programme under Grant Agreement No 101004730.
Acknowledgements:
The authors want to acknowledge the industrial partners that made possible the realisation of the CCM: Brevetti Bizz during the R&D and Nanoker in the prototyping and production phase. We also kindly acknowledge the HL-LHC WP5 “Collimation”, and in particular the CERN groups BE-ABP, SY-STI and TE-VSC for the support in the development, production and testing of MoGr for use in the LHC collimation system. A big support was received from the CERN colleagues from EN-MME, in particular the Mechanical Laboratory, for the thorough characterisation of the materials and for the precious suggestions on the directions of improvement.
Finally, a big thank goes to A. Bertarelli, J. Guardia and N. Mariani, that initiated this thread of research, and to M. Losasso and M. Vretenar for the guidance within I.FAST.