The use of accelerated particles is now an established medical technique for cancer therapy, providing to the radiation oncologists an alternative tool for the fraction of tumours that are not curable with conventional X-rays. Heavy ions, like carbon, are effective for some tumours resistant to X-rays and protons, but their use is so far limited by the size and cost of the required infrastructure, mainly synchrotron and gantry – the beam delivery system.
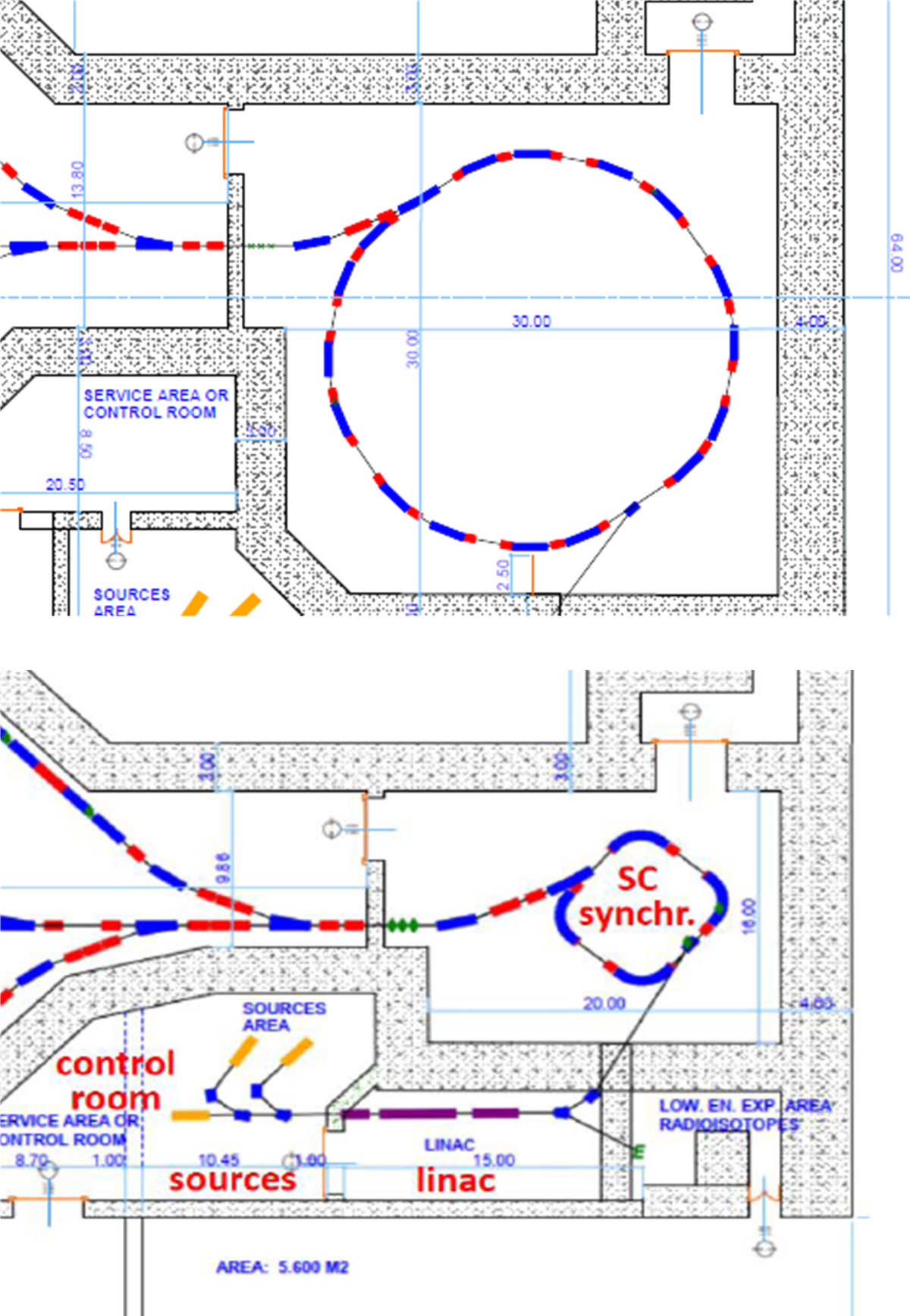
In order to reduce the machine and gantry footprint and cost, various European initiatives, as SIGRUM and the advanced version of SEEIIST, are planning to use an advanced ion gantry and, eventually, a synchrotron based on Nb-Ti superconducting (SC) magnets, a cheaper option compared to conventional solutions based on resistive magnets (Fig. 1).
More recently, two projects funded under Horizon 2020, HITRIplus and I.FAST, have launched a collaboration to investigate the next generation of ion therapy magnets both for gantry and for accelerator as they have both obtained funding for work packages on superconducting magnets.
The Heavy Ion Therapy Research Integration plus (HITRIplus) brings together all four European ion therapy centres with leading EU industries, academia, and research laboratories. Its WP8 (Superconducting Magnet Design) will explore a novel, robust, cost-effective magnet design for a light rotatable gantry and for the accelerating synchrotron. As of now, it is reviewing possible solutions and assessing the use of various types of superconductor and magnet layouts. The collaboration will then design, manufacture and test a magnet demonstrator, which will be a curved CCT (Canted Cosine Theta) dipole, wound with classical Nb-Ti.
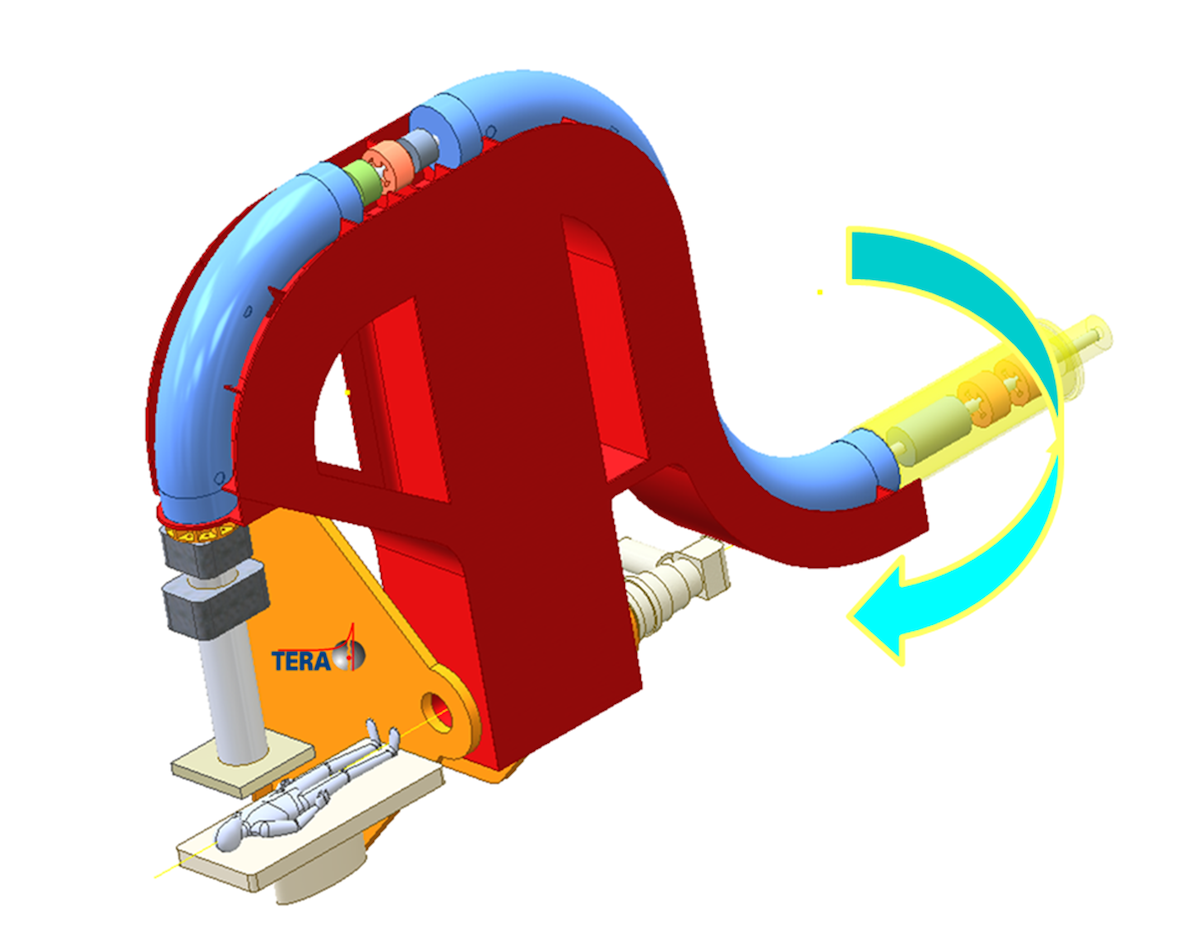
Continuing the tradition of FP6-CARE, FP7-Eucard, FP7-Eucard2 and H2020-ARIES programs, the Innovation Fostering in Accelerator Science and Technology (I.FAST) is a vast program consisting of 48 members, mostly being Research Institutes and Universities active in the field of particle accelerators. Similarly to HITRIplus program, I.FAST has a work package on superconducting magnets, WP8 (the number is pure coincidence), with the same research institutes of HITRIplus WP8. Its scope is to study the CCT magnet design in High Temperature Superconductor (HTS) together with industry, for particle therapy with hadrons (namely heavy ions). I.FAST WP8 has the goal to bring the HTS CCT technology to maturity to allow for a later design of a full HTS system. If successful and if the time scale fits, HTS technology will be operating at higher temperature than 5 K with consequent simplification of the cooling system and energy saving.
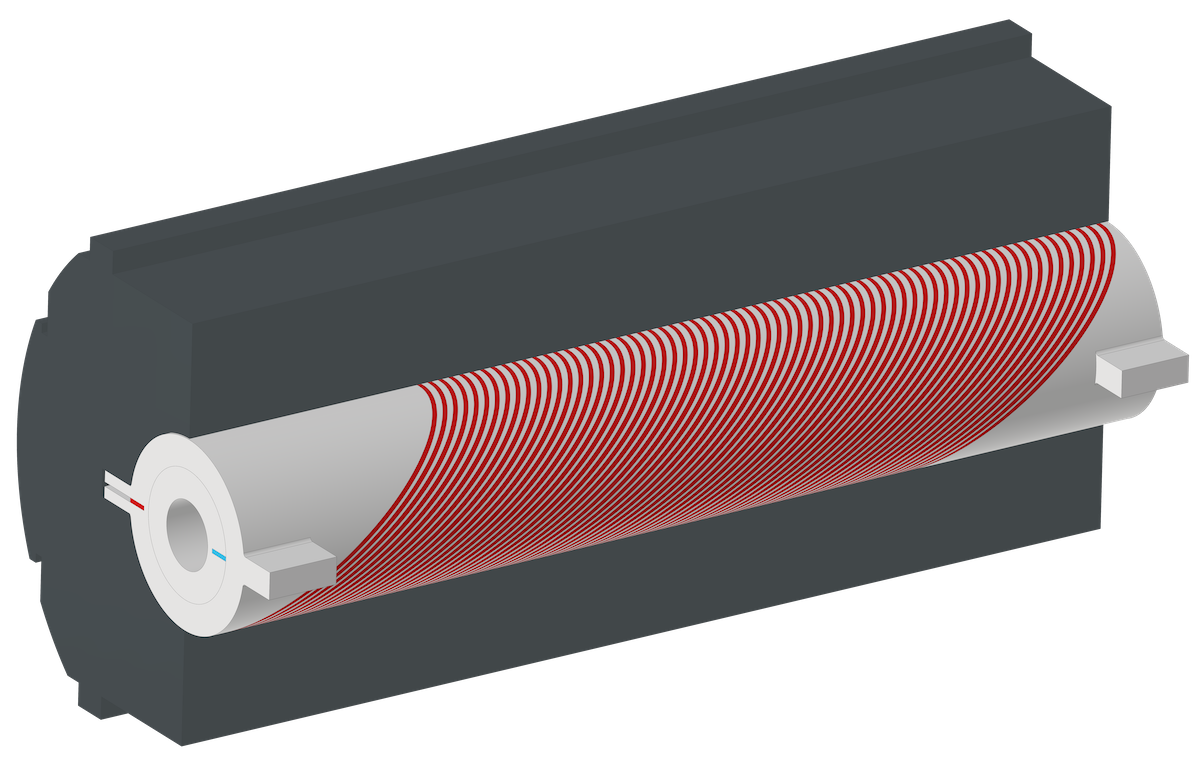
With 15 meetings held in less than a year (eight for HITRIplus and seven for I.FAST), the collaboration between the research institutes is progressing well. The participants have selected common targets for the magnet: 80 mm of free bore, 4 T of central field with a field ramp rate of about 0.4 T/s. Performance of the various design options are being evaluated against these targets, which are suitable for a gantry application for carbon ion therapy with beam rigidity of B*ρ = 6.6 Tm, corresponding to the fully stripped ion energy of 430 MeV/nucleon, where the curvature radius of the gantry, ρ, is 1.65 m for field of 4 T.
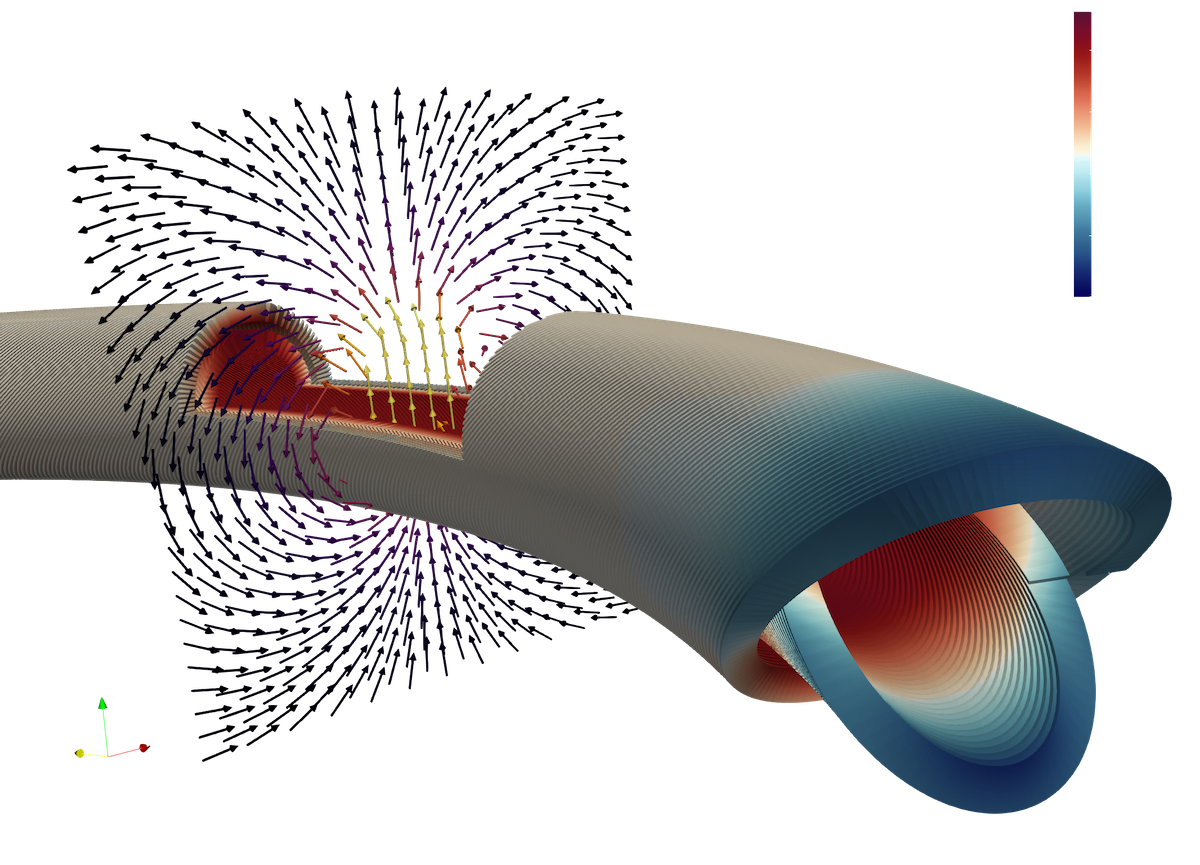
While HITRIplus and I.FAST will share a common thermal design, both will develop CCT type magnets with different topology and material. I.FAST is working on two straight CCT magnets, the first one is a combined function (dipole + quadrupole) magnet based on Nb-Ti with fine filaments for low losses (sketch in Fig. 3), and the second one, the main outcome, is a straight CCT based on HTS. HITRIplus has taken up the challenge to build a curved magnet demonstrator with a very small bending radius of 1.65 m. The provisional baseline of HITRIplus is to have Nb-Ti conductor wound as CCT (Fig. 4), conduction cooled with impregnation, since HTS technology is not yet mature to be tested in a curved geometry proven (it is the job of I.FAST to prove it, however in a simpler straight shape). For both programs, due to indirect cooling and ramped operation, the thermal design will be more critical than for the usual steady state operating mode with wet coil layout.