Electron linacs are key components of many research, medical, and industrial facilities, ranging from light-sources and FELs, to radiotherapy and industrial systems. In many cases their size is a limiting factor, impacting the footprint, cost and in some case their performance. Making them more compact would open many new possibilities.
It may seem counter-intuitive but the answers might come from one of the largest linacs ever designed. Very long, since it would stretch from 11 to 50 km, but nevertheless compact given its energy reach. The CLIC study prepares an option for a 380 GeV Higgs/top accelerator facility hosted at CERN which can be subsequently upgraded to achieve collisions at 1-3 TeV energies.
There are clear synergies between the R&D invested into CLIC in developing high gradient, intense beam, and nanobeam technologies and the technologies needed for compact accelerator solutions in research, medical and industrial applications. Also, the CLIC beam-dynamics methodology and studies are excellent tools for optimising the performances of compact linacs in these application spaces. Widespread adoption of X-band technologies has reciprocally important direct and indirect benefits to the CLIC studies as it provides increased industrial awareness, readiness, and capabilities for the core CLIC technologies.
Electron linac technology for novel cancer treatment
An exciting application of high-performance electron linac technology is so-called FLASH radiation therapy. FLASH therapy consists of irradiating cancer tissues with very high dose rates, in the range of hundreds of Gy/s, so that an entire treatment can be given in a tenth of a second. This gives a biological effect that results is less toxicity for healthy tissue while maintaining tumour control.
A clinical FLASH facility based on 100 MeV-range electrons accelerated using CLIC-derived technology is being developed in a collaboration between CERN and the Lausanne University Hospital (CHUV). In 2023, the project moved forward towards a final technical design, laying the ground for construction by an industrial partner, THERYQ. The excavation of the site of bunker at CHUV is underway.
Linacs for medical and industrial imaging
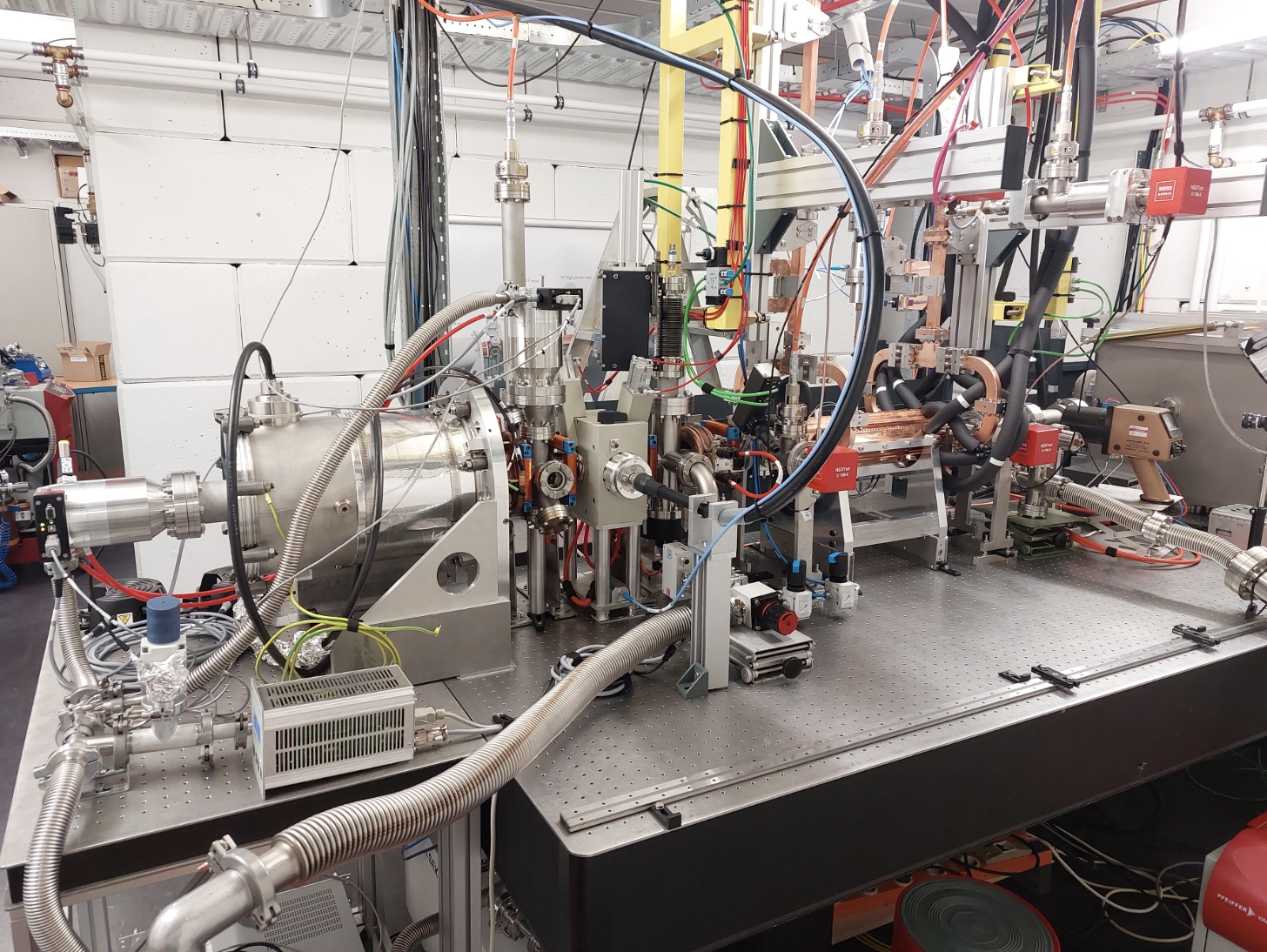
Compact Inverse Compton Scattering (ICS) facilities based on X-band technology are another developing avenue for the use of CLIC technology for medical and industrial applications. The range of parameters of the generated light provides imaging capabilities that can only be found in much larger synchrotron facilities. The reduced footprint of X-band-based ICS facilities allows them to be installed locally in research, medical, or industrial environments.
A first facility has been built and put into operation by TU Eindhoven. At CERN, experimental tests at CFT2 are planned for 2024. The aim of these tests is to increase the brilliance and overall performance of such facilities. In this setup, X-rays within reach of biological applications will be produced in less than two meters of length. A facility in Tsinghua University making use of X-band acceleration is also being completed and commissioned this year.
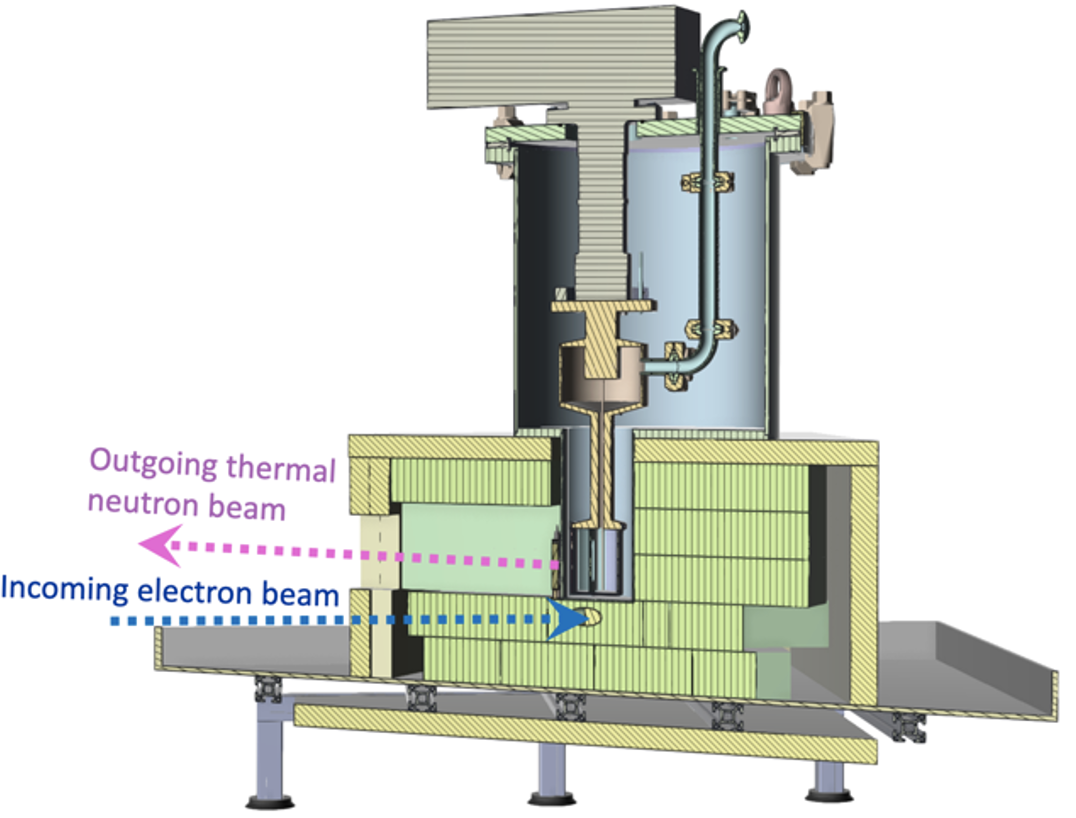
A concept study for using a compact electron linac to drive the production of thermal neutrons as part of a compact, low-cost facility has also been initiated with an industrial partner, DAES. Such thermal neutrons have Angstrom-scale wavelengths and so can be used to probe materials at the atomic scale using techniques similar to X-ray crystallography. The advantage of imaging with neutrons, however, lies in their ability to penetrate deeply into materials and to ‘see’ low-Z elements such as hydrogen.
Cold neutrons find many uses cases in industrial scenarios. They can be used to undertake in-situ and in-operando measurements of batteries and fuel-cells in order to directly optimise their geometries and material composition for combatting the causes of aging. They can also be used to measure, understand and mitigate the causes of residual stresses generated by the manufacture, welding, use, and repair processes of a bulk component. These in-demand diffractometry applications require high fluxes of cold neutrons and by using high-gradient technology, a compact facility is within reach.
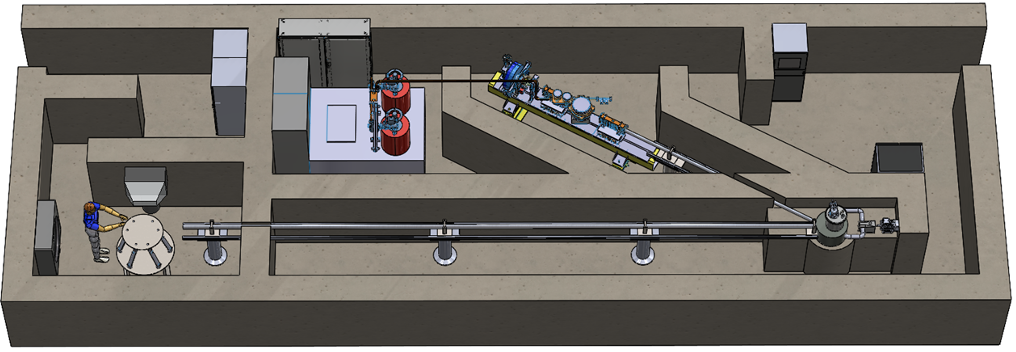